As a common metal casting process, die casting can create high-quality, durable parts and exact dimensions.Because of it’s particularity. Die casting can meet customers’ complex customization needs. This article will introduce to you about die casting’s four characters.
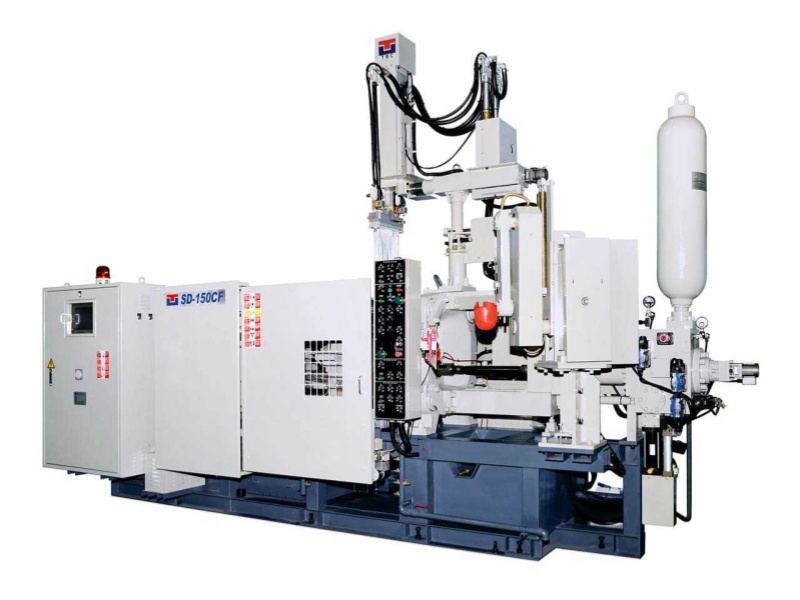
Die casting is a manufacturing process that allows the production of metal parts with a high degree of precision. In this casting process, molten metal is injected into a mould, where it cools and hardens to create the desired shape.
The method can be used to create various metal parts, from gears and engine blocks to door handles and automotive parts.
What materials are often used in die casting?
Aluminum alloys are by far the most important materials in volume die-cast production. They respond best to a hot chamber and high pressure—or more recently vacuum die casting—and provide moderate to high strength and high precision parts. Commonly used aluminum alloy models:
Aluminium 46100 / ADC12 / A383 / Al-Si11Cu3
Aluminium 46500 / A380 / Al-Si8Cu3
A380-Part-with-Red-Anodizing
Magnesium
Magnesium alloys are widely used for lightweight and high-strength parts. There are limitations in the processing, but magnesium alloys can achieve among the thinnest sections in die casting, because of very low viscosity in the melt. Commonly used magnesium alloy models:
Magnesium AZ91D, AM60B, and AS41B
Zinc
Zinc is very widely die-cast for many lower-strength applications. Zinc alloys’s major constituent of are low-cost, easily cast, and sufficiently strong for many components such as enclosures, toys, etc.
Copper
Copper is not widely used in die casting, as it has a tendency towards cracking. It requires a high melt temperature, creating increased thermal shock in the tooling. When it is die-cast, it requires careful handling and a high-pressure process. Here is a product of copper we used to made.
Advantages of Die Casting
When you need to comes to mass-producing metal parts, die casting is one of the most efficient and cost-effective methods. It’s a process that has been around for centuries, but its popularity has grown in recent years as manufacturers seek ways to reduce production costs.
Here are some of the advantages of die casting:
Complex shapes: Die casting is a process that can produce complex shapes with tight tolerances.
Versatility: The process is versatile and can be used to cast a variety of metals, including aluminium, zinc, and magnesium.
High production rate: It is a relatively fast process, which can be an advantage when time is of the essence.
Cost-efficient: The process is also relatively inexpensive, making it a cost-effective option for many applications.
Repeatability: It also allows for a high degree of repeatability, meaning that parts can be manufactured to precise specifications.
Applications of Die Casting
Toys: Many toys were formerly manufactured from die-cast zinc alloys such as ZAMAK (formerly MAZAK). This process is still widely used despite plastics taking over much of the sector.
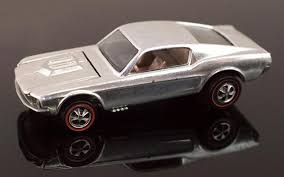
Automotive: Many ICE and EV car parts are made by die casting: major engine/motor components, gears, etc.
Furniture Industry: It is also used in the furniture industry. It’s often used to create furniture hardware such as knobs.
Electronics: Enclosures, heat sinks, hardware.
Telecommunication-Die-Casting-Parts
Many other industries use die-casting processes for medical, construction, and aerospace industries. It is a versatile process that can be used to create various parts and products.
Die casting is a manufacturing process that has been around for centuries and continues to be popular because of its versatility and ability to create complex shapes. The process can be used to create metal parts for a variety of industries, including automotive, aerospace, furniture, and appliance manufacturing.
If you have any requirement please contact us!we will try our best to help you to solve the problem.
Post time: Mar-20-2024