CNC and Injection as the two most be popular crafts for manufacture, which both can make the high-quality product or parts in each areas and they have their own advantages and disadvantages. So how to choose the best way for project can be a challenge. But as a professional manufacture, this article will show you their strengths and weaknesses, and how to determine which is right for your project.
CNC Machining
CNC can be simply described as asubtractive manufacturing process that uses computer-controlled machines to remove material from blocks of raw materials to create finished parts or products. The process involves entering the design into a computer program that controls the movement of the machine to carve out the desired shape. You can also read our guide about CNC to know more information.
Strengths
CNC has a natural advantage in making metal parts. A variety of tool heads can grind parts very finely, and CNC can do a good job whether it is a large product or a small part.
At the same time, CNC also has more flexibility in material selection. Whether it is a series of common metals such as aluminum, copper, iron, alloy, or common materials such as ABS and resin, they can be fine-processed by CNC equipment.
At the same time, CNC is also equipped with two types, three-axis and five-axis. The common manufacturers may choose to use three-axis for product processing for cost considerations, but as a professional metal manufacturer, Ruicheng is equipped with a five-axis CNC machine tool, which can complete product production better and faster.
Weaknesses
One of the main disadvantages of CNC machining is its high cost, especially for low-volume production. CNC machines require specialized programming and setup and are expensive to purchase and maintain. Additionally, CNC machining can be very time-consuming, with longer lead times than other manufacturing methods. So CNC can more suit designer to make sample at the early stage of design.
Injection Molding
Injection molding is one of the most mainstream manufacturing processes in the current market. It usually involves injecting a resin or plastic compound (such as ABS, PP, PVC, PEI) into a molten state and then cooling it to form the desired product or part. Now this process has highly automated and can produce a large number of parts quickly and efficiently. If you want to know more about injection, please contact us anytime.
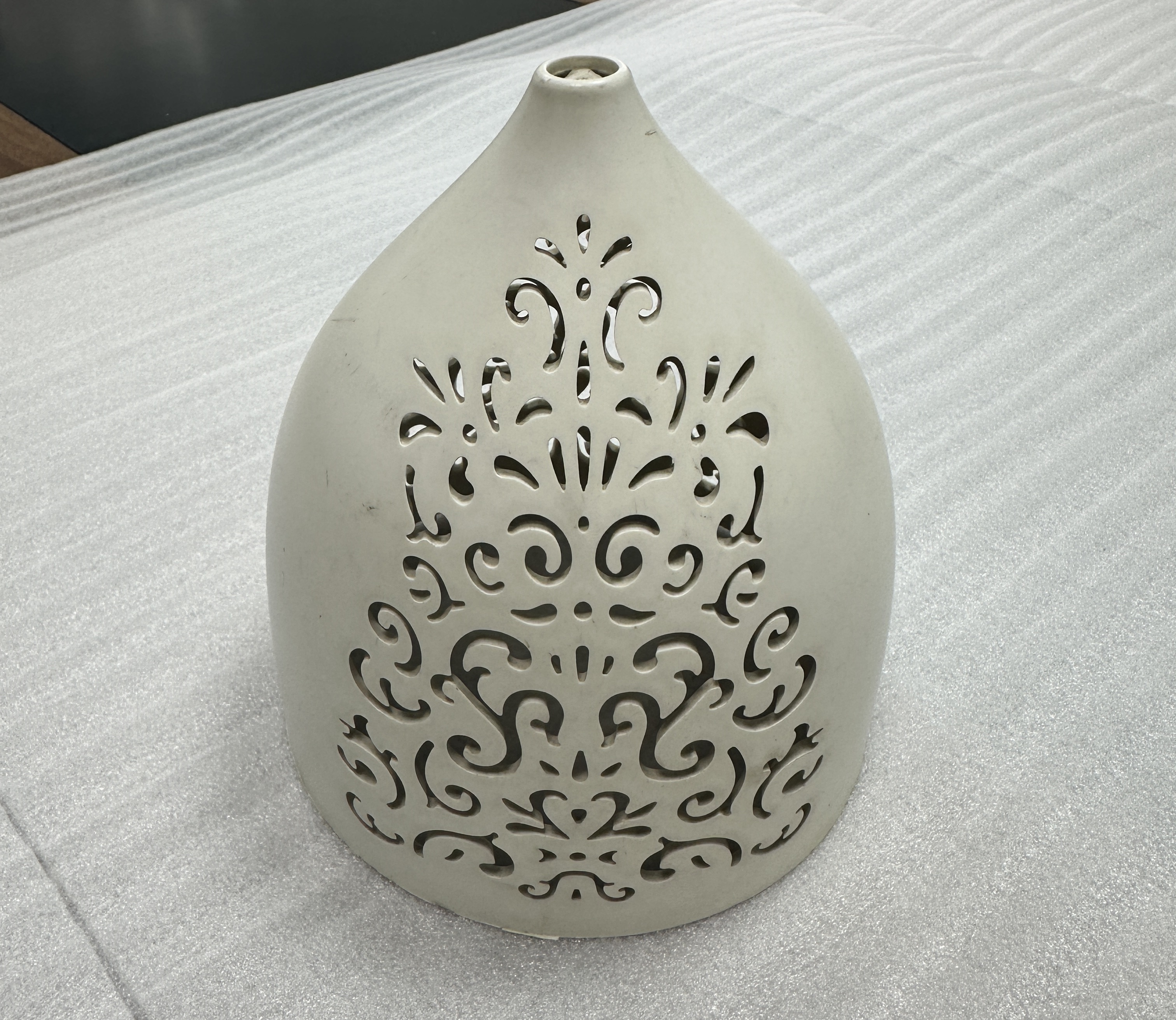
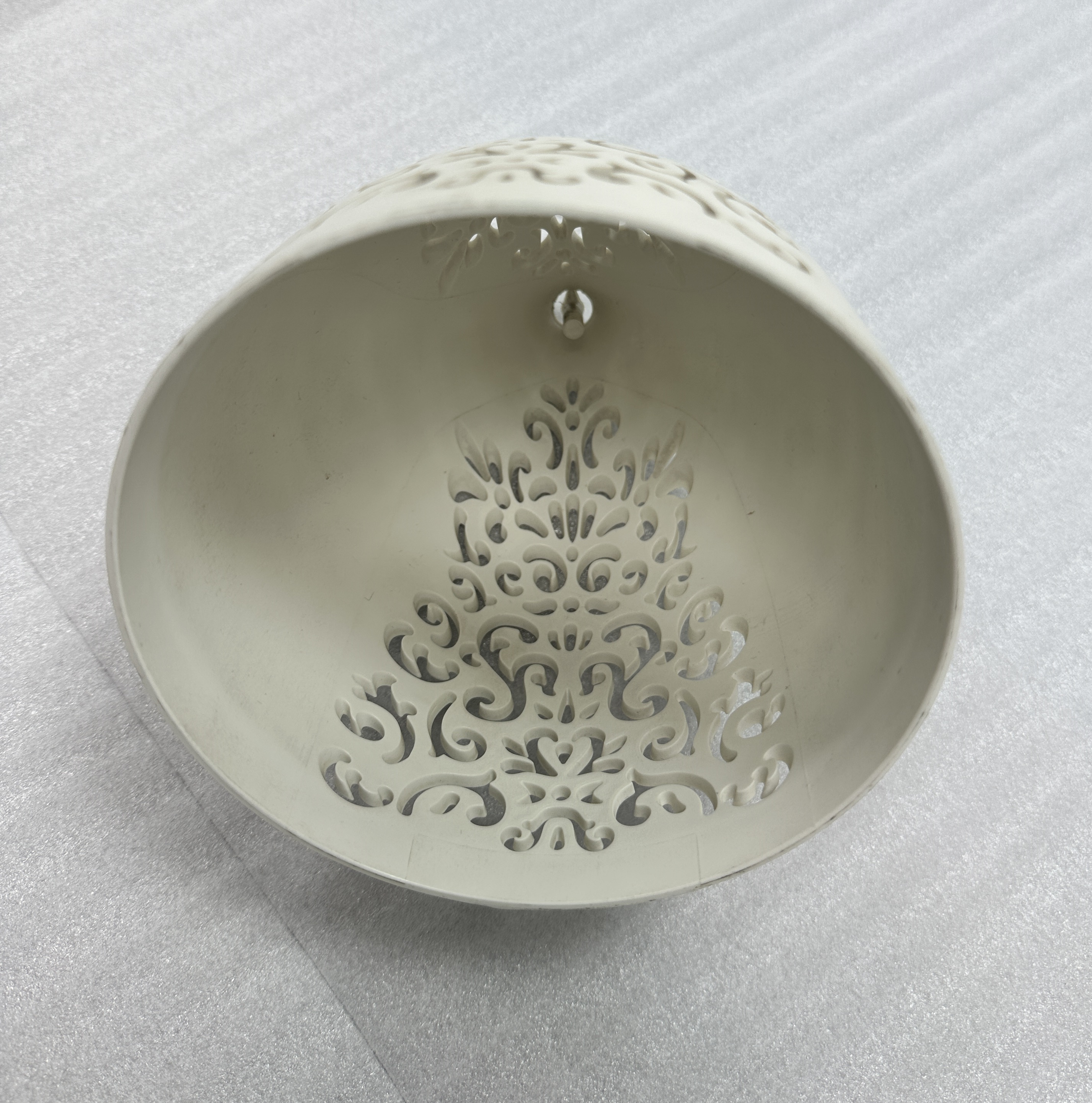
Strengths
The biggest advantage of injection molding is that it can produce a large number of parts quickly, and because of its high degree of automation, it does not require too much manual participation, so the unit cost is low. In terms of material selection, almost all plastic compounds can be used as raw materials for injection molding, which gives it a unique advantage in the production of plastic products. With the advancement of technology, injection molding can also produce parts with complex geometries and precise details.
Weaknesses
One of the main weaknesses of injection molding is the high initial mold cost. Injection molds are expensive to design and produce, and it needs professional to do this work. That's making low-volume production difficult to achieve cost-effectively. Additionally, the process is not as flexible as CNC machining because it is difficult to make design changes once the mold is produced.
Different points
There are some different point between injection and CNC:
1.Manufacturing Process: Injection is a manufacturing process where molten material is injected into a mold or cavity to create a desired shape, while CNC (Computer Numerical Control) involves the use of computer-controlled machines to precisely cut and shape materials based on pre-programmed instructions.
2.Material Usage: Injection is commonly used for materials like plastic or metal, where the molten material is injected into the mold to form a solid product. CNC, on the other hand, can be used with various materials such as metal, wood, plastic, and composites, allowing for a wider range of applications.
3.Automation Level: Injection molding is a highly automated process, where the material is injected into the mold using specialized machinery. CNC, while still automated, requires the programming of instructions for tool movements and material removal, offering more flexibility and customization.
4.Complexity and Precision: Injection molding is capable of producing complex and intricate shapes with high precision, especially when using advanced molds. CNC machining also offers precision, but its level of complexity and precision depends on the programming, tooling, and machine capabilities.
5.Batch Size and Repetition: Injection molding is well-suited for mass production, allowing for the creation of large quantities of identical parts with minimal variation. CNC machining can handle both small and large production runs, but it is more flexible for producing customized or low-volume parts.
6.Tooling and Setup: Injection molding requires the creation of molds, which can be expensive and time-consuming initially but offer long-term cost efficiency for large-scale production. CNC machining requires the setup of appropriate tooling, including cutting tools, fixtures, and workholding, which can be more adaptable for different part designs and production needs.
7.Waste and Material Efficiency: Injection molding can generate waste in the form of excess material, sprues, and runners, which may need to be recycled or disposed of. CNC machining typically produces less waste as it removes material selectively based on the programmed instructions.
Summary
CNC machining and injection molding are valuable manufacturing processes, each with their own pros and cons. Deciding which process to use depends on a variety of factors, including the complexity of the part or product, required accuracy, throughput, and budget. By understanding these factors and working with a qualified supplier like NICE Rapid, companies can decide which manufacturing process is right for their specific project.
Post time: Jun-05-2024