Placing gates and injection molding sprue is a crucial part of the injection molding process. The placement of these components can affect the quality of the final product, as well as the efficiency of the process. In this article, we will explore more about the placement of gates and injection molding sprue, as well as the material flow and how to release air safely.
Firstly, let us understand what gates and injection molding sprue are. A gate is a small opening in the mold through which the molten plastic is injected. The size and placement of the gate can affect the material flow and the final product's quality. The injection molding sprue is the channel through which the molten plastic enters the mold cavity.
The placement of gates and injection molding sprue is critical in the injection molding process. The gate location should be carefully chosen to ensure that the plastic flows evenly throughout the mold cavity, and the part fills completely. If the gate is too small, the plastic may not flow well, leading to incomplete filling of the mold cavity, resulting in defects in the final product. If the gate is too large, it may leave visible marks on the final product, known as gate vestiges.
Material flow is another critical factor in the injection molding process. The molten plastic needs to flow evenly throughout the mold cavity to ensure that the part fills completely. To achieve this, the injection molding sprue should be placed in a location that allows the plastic to flow evenly throughout the mold cavity. The sprue should also be of sufficient size to allow the plastic to flow easily.
To ensure that the plastic flows evenly throughout the mold cavity, the mold design should be optimized. The design should include features such as uniform wall thickness, which helps to ensure that the plastic flows evenly throughout the mold cavity. The mold should also have sufficient draft angles, which help to ensure that the part can be easily ejected from the mold.
Air release is another important factor in the injection molding process. Air trapped inside the mold can cause defects in the final product. To release air safely, the mold should have venting channels that allow air to escape. The venting channels should be strategically placed to ensure that air can escape without affecting the final product's quality.
In conclusion, placing gates and injection molding sprue is a critical part of the injection molding process. The gate location and size, as well as the injection molding sprue's placement, can affect the material flow and the final product's quality. The mold design should be optimized to ensure that the plastic flows evenly throughout the mold cavity, and the mold should have venting channels to release air safely. By paying attention to these factors, can produce high-quality injection-molded parts efficiently.
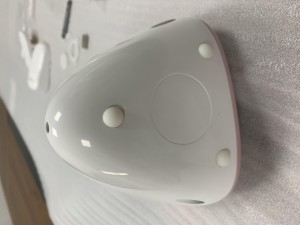
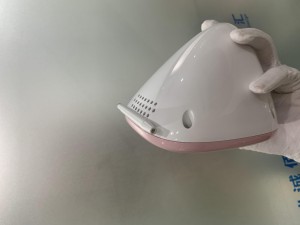
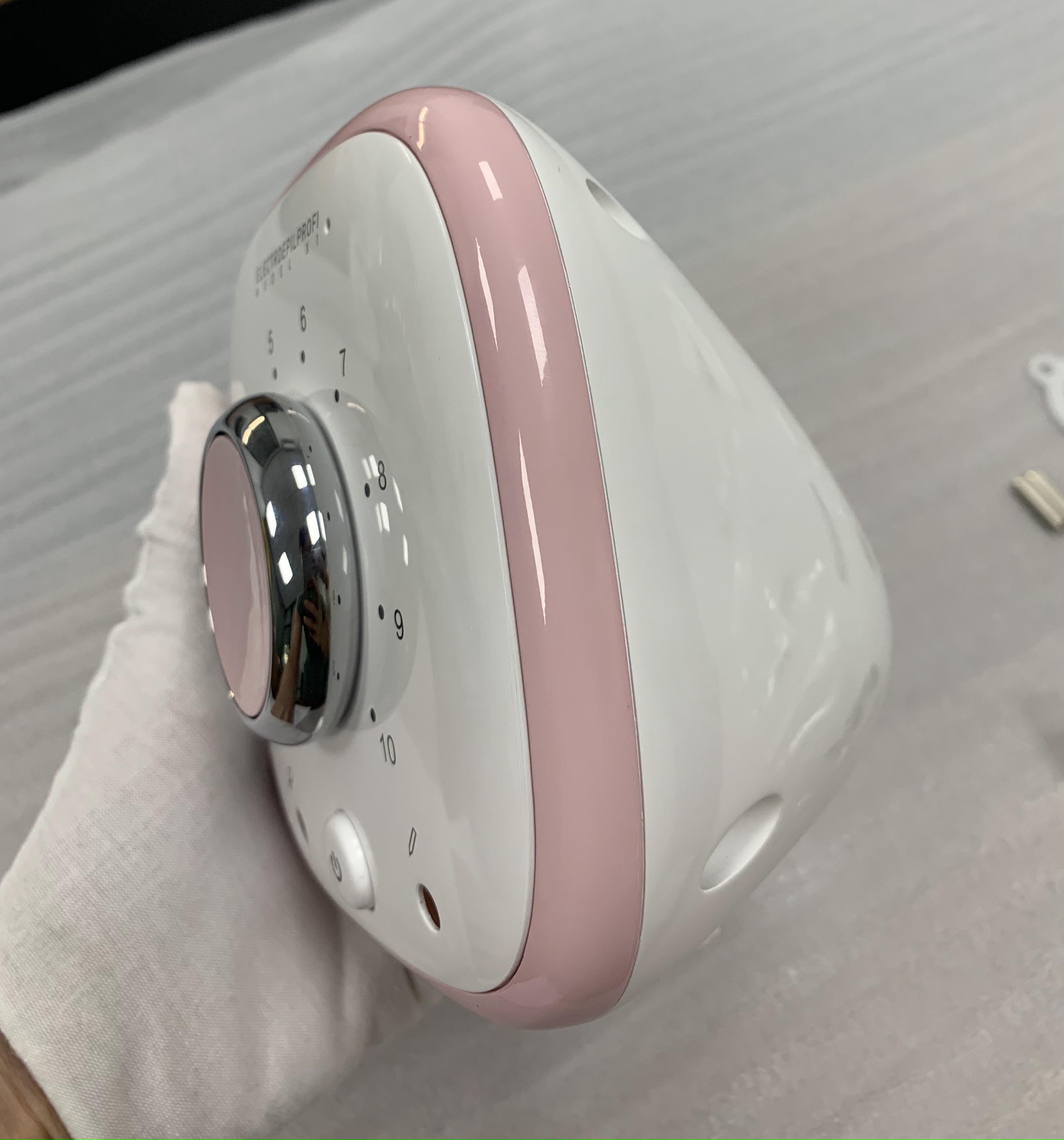
If you want to learn more ,please feel free to contact us ,then we'll provide the free consultant for you and show some case we have made for your reference .
Post time: Jun-14-2023