What is a Progressive Mould?
A progressive mould (also known as a progressive die) is a specialized tool used for continuous stamping and shaping of parts. The core principle of this mould lies in performing multiple operations on the material within the same mould across various stations. As the material moves through each station, different operations such as cutting, shaping, or punching are carried out, eventually resulting in a fully formed part. Each station performs a specific task, and as the material progresses, multiple steps are executed in sequence, leading to the completion of the final product.
While progressive moulds are typically used in metalworking, such as in metal stamping, the same principle can be applied in injection moulding. By utilizing different parts of the mould for continuous and complex material processing, this method ensures efficiency, precision, and consistency in the production process.
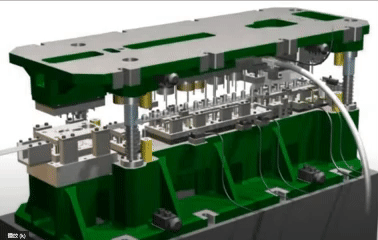
How Does a Progressive Mould Work?
In a progressive mould, the process usually starts with a coil of raw material fed into the mould, with a press advancing the material through various stations. At each station, a specific operation is performed, such as punching, bending, or cutting. Once one cycle of pressing is complete, the material moves forward to the next stage, and the previous steps repeat, allowing for continuous processing. By the time the material passes through all the stations, it results in a fully formed and finished part.
This multi-stage design is ideal for high-volume production as it consolidates multiple operations into one mould, reducing the need for repeated setups and handling, thus greatly increasing production efficiency.
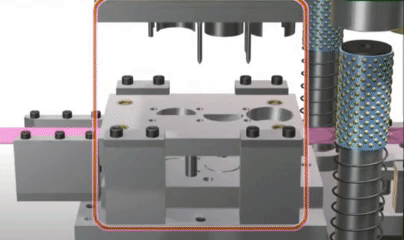
The Advantages of Progressive Moulds
1.High Production Efficiency:Progressive moulds allow for multiple operations to be performed on a single production line, eliminating the need for repeated material handling and positioning across different machines. This greatly reduces production time and increases the number of parts produced per hour, making it an excellent choice for mass production.
2.Consistency and Precision:Since the material is processed through multiple stations within the same mould, there is minimal error in production. This ensures that each part is made with high precision and consistency, especially for products that require strict tolerances and dimensional accuracy.
3.Material Saving:Progressive moulds can be optimized according to the size and shape of the product to minimize material waste. By precisely controlling the stamping process, material utilization is significantly improved, helping reduce production costs.
4.Reduced Labor Costs:As multiple operations are completed within a single mould, the need for manual intervention is greatly reduced. This automated production process decreases the number of operators required and also minimizes errors and material wastage caused by human handling.
5.Ideal for Complex Parts:Progressive moulds are particularly suited for manufacturing complex parts that require multiple processes. Through continuous operations at different stations, these complex processes can be completed efficiently and accurately without compromising product quality.
Applications of Progressive Moulds in Various Industries
Progressive moulds are widely used across various industries, particularly in metalworking, automotive manufacturing, and electronics production. They are ideal for producing small precision parts, such as automotive components, electronic enclosures, and appliance parts. For parts that require high precision and large-scale production, progressive moulds are the preferred solution.
In the injection moulding industry, the concept of progressive moulds can be applied to multi-cavity moulds and complex structural parts. By performing multiple injections or combined moulding processes, manufacturers can achieve precise structural requirements and surface treatments.
Conclusion
Thanks to their efficiency, precision, and high material utilization, progressive moulds have become an indispensable tool in modern manufacturing. For industries that require high-volume production with stringent precision and consistency, progressive moulds are an ideal solution. Through optimized mould design and production processes, companies can significantly improve production efficiency, reduce costs, and ensure product quality stability.
If you’re looking for an experienced injection mould manufacturer to provide progressive mould solutions, Ruicheng can help address your production challenges. Contact us to learn more about our mould design and manufacturing services.
Post time: Oct-21-2024