What is Metal Extrusion?
Metal extrusion is a widely-used manufacturing process in which a metal billet is forced through a die to create objects with a fixed cross-sectional profile. The process is akin to squeezing toothpaste from a tube: as the metal is pushed through the die, it adopts the shape of the die opening. This method is primarily used to produce long parts with consistent cross-sections and is particularly well-suited for materials such as aluminum, copper, magnesium, and steel.
Extrusion allows manufacturers to create a wide range of shapes, from simple rods and tubes to more complex profiles like window frames and intricate machine parts. It is a highly efficient process that can be adapted to various materials and applications, making it essential in industries such as automotive, aerospace, construction, and electronics.
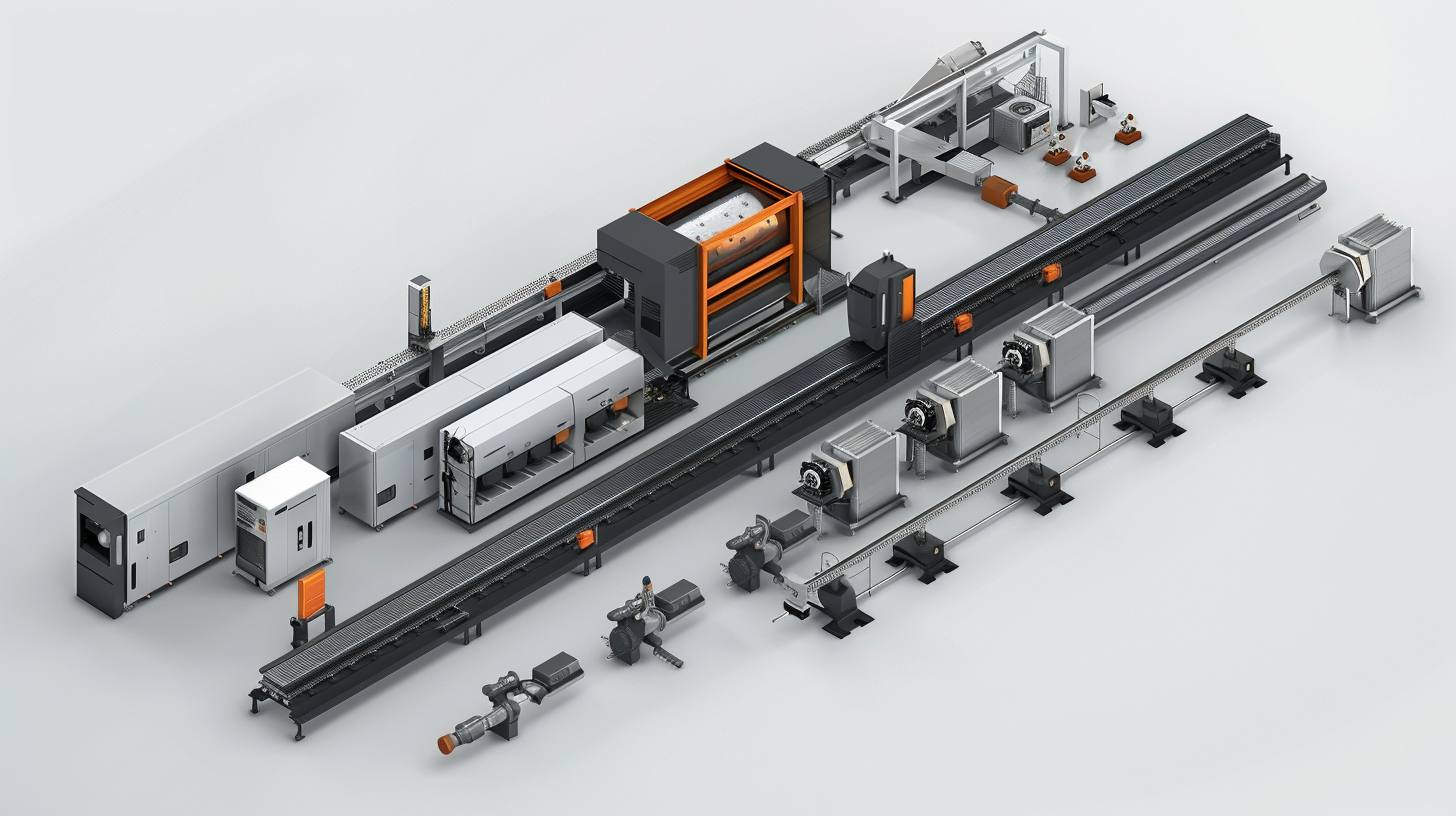
The Extrusion Process
The extrusion process involves several key steps. First, a cylindrical billet of metal is prepared, often preheated to make the material more malleable and easier to shape. This is particularly important in hot extrusion, where the billet is heated to reduce the force needed to push the material through the die. Once prepared, the billet is placed into an extrusion press, where a hydraulic ram forces it through the die opening.
As the metal flows through the die, it takes on the shape of the die’s cross-section, producing a continuous length of material with a uniform profile. After the extrusion exits the die, it is cooled, typically using air or water, and then cut to the desired length. Depending on the material and the intended application, additional post-processing steps such as heat treatment, machining, or surface finishing may be required to meet specific product requirements.
Types of Extrusion
Extrusion can be categorized into several types based on how the metal flows through the die:
1.Direct (Forward) Extrusion: In this method, the billet is pushed directly through the die, and the metal flows in the same direction as the force applied by the ram. This is the most common form of extrusion but requires significant force due to the friction between the billet and the container walls.
2.Indirect (Backward) Extrusion: Here, the die moves toward the billet, causing the metal to flow in the opposite direction of the applied force. This method reduces friction and, consequently, the amount of force required, making it more energy-efficient than direct extrusion.
3.Hot Extrusion: This process involves heating the billet to a high temperature, which makes the metal easier to shape and reduces the risk of cracking or material fatigue. Hot extrusion is commonly used for metals like aluminum and magnesium, which are easier to work with at elevated temperatures.
4.Cold Extrusion: In contrast, cold extrusion is performed at or near room temperature. This method is often used to improve the strength of the final product through work hardening. Cold extrusion is typically used for materials such as copper, steel, and aluminum for parts that require high precision.
Each type of extrusion has its own advantages, with the selection of method depending on the material being used, the complexity of the shape, and the specific requirements of the application.
Advantages of Metal Extrusion
The key advantage of metal extrusion is its ability to produce long, continuous parts with consistent cross-sectional shapes. This makes it ideal for industries that require large quantities of precisely shaped components. The process is also highly versatile, as it can handle a wide variety of metals and produce both simple and complex shapes. Moreover, extrusion is an efficient process that generates minimal waste, as the material is forced into the desired shape rather than being removed, as with machining.
Extrusion also offers enhanced material properties. For instance, hot extrusion can improve the ductility and toughness of metals, while cold extrusion can increase material strength through work hardening. Additionally, the process allows for the production of custom shapes that meet the unique needs of different industries, making it a valuable tool for manufacturers seeking to create specialized components.
Applications of Extrusion
Extrusion has a wide range of applications across various industries due to its versatility and precision.
In the automotive industry, extruded aluminum parts are used to reduce the overall weight of vehicles, improving fuel efficiency without compromising structural integrity.
In the construction sector, extruded components like window frames, structural supports, and door frames are valued for their durability, ease of assembly, and resistance to corrosion.
In electronics, extrusion is commonly used to create heat sinks, enclosures, and connectors due to the excellent thermal and electrical conductivity of materials like aluminum and copper.
In the aerospace industry, extruded components made from lightweight yet strong metals such as titanium and aluminum are essential for reducing aircraft weight while maintaining performance and safety standards.
These examples highlight how extrusion plays a crucial role in many industries, delivering cost-effective, high-quality solutions for a wide range of applications.
Challenges in Metal Extrusion
While extrusion offers numerous benefits, the process is not without its challenges. One of the main difficulties is ensuring consistent quality across long production runs. Since the material is forced through the die under significant pressure, any inconsistency in the force or die design can result in defects such as uneven profiles or surface irregularities. Additionally, controlling the temperature and cooling rates is critical to prevent warping or cracking in the finished product.
Another challenge is the design of the die itself. Since the die determines the shape of the extruded material, any flaws in the die design can lead to poor-quality products. Developing a well-designed die requires precision engineering and careful consideration of the material’s properties and the intended application.
Conclusion
Metal extrusion is a versatile and efficient manufacturing process that enables the production of complex and consistent profiles across a range of industries. By understanding the extrusion process, types, and advantages, manufacturers can leverage this technique to create high-quality components tailored to their specific needs. While the process does come with its challenges, advancements in technology and careful process control continue to make extrusion a reliable and essential method for producing metal parts.
Whether it's in the automotive, aerospace, electronics, or construction industries, extrusion remains a cornerstone of modern manufacturing, offering solutions that are both cost-effective and precise.
Post time: Sep-06-2024