Weld lines are a common defect in injection molding that occur when two flow fronts of molten plastic meet but fail to fully bond. These lines not only affect the appearance of the part but can also weaken its structural integrity. To avoid weld lines in injection molding, focus on optimizing mold design, adjusting process parameters, using the right material, and controlling melt flow.
Let’s explore the causes of weld lines and effective strategies to minimize or eliminate them.
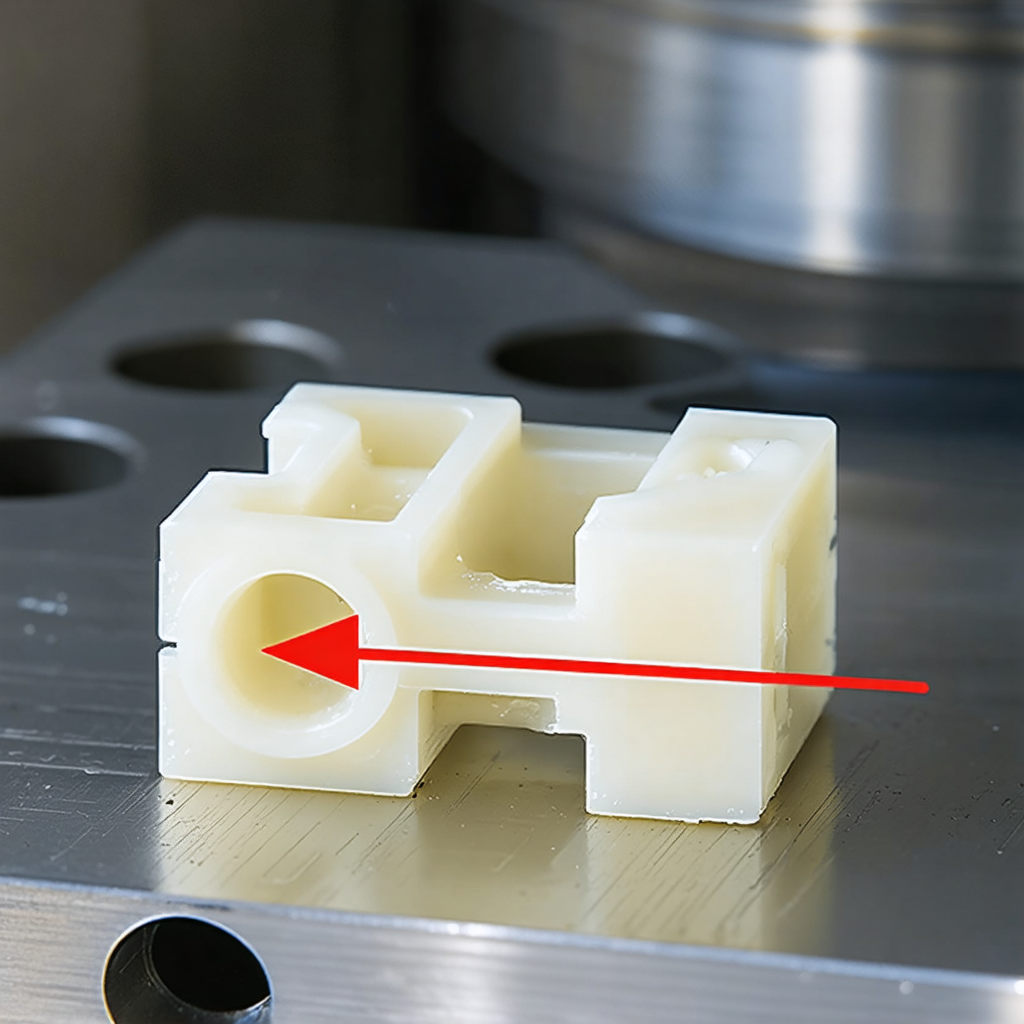
What Causes Weld Lines?
Weld lines occur when separate molten plastic flow fronts converge but fail to merge seamlessly, leaving a visible line or a weak spot. This can happen due to insufficient temperature, low pressure, or poor mold design that disrupts material flow.
Think of it like pouring water into a pool from two hoses. If the streams don’t merge smoothly, they’ll leave a distinct ripple where they meet. Similarly, in injection molding, if flow fronts don’t fully meld, a visible weld line forms.
Key Strategies to Avoid Weld Lines
1.Optimize Mold Design
A well-designed mold ensures consistent material flow, reducing the likelihood of weld lines.
Gate Placement:Position gates strategically to minimize the meeting of multiple flow fronts.
Runner Design:Use balanced runners to ensure uniform flow across the cavity.
Ventilation:Add vents to release trapped air that can disrupt flow fronts.
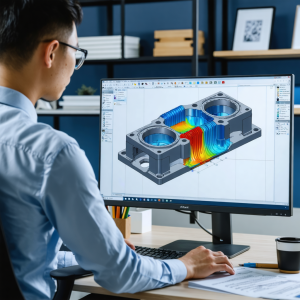
2.Adjust Process Parameters
Fine-tuning processing conditions can help flow fronts merge seamlessly and avoid weld lines.
Increase Melt Temperature: Higher melt temperatures improve flowability, allowing flow fronts to bond properly.
Raise Injection Speed: Faster injection speeds reduce cooling time, enabling better merging of flow fronts.
Optimize Packing Pressure: Sufficient packing pressure ensures complete filling and minimizes defects.
Parameter | Effect on Weld Lines | Suggested Adjustment |
---|---|---|
Melt Temperature | Improves bonding of flow fronts | Raise within safe limits |
Injection Speed | Reduces premature cooling | Increase slightly |
Packing Pressure | Ensures complete cavity filling | Optimize for full bonding |
3.Use the Right Material
Material selection plays a significant role in avoiding weld lines.
Low-Viscosity Materials: These flow more easily, reducing weld line visibility.
Reinforced Materials: Additives like glass fibers improve structural integrity but may require higher processing temperatures to reduce weld lines.
Pigmented Resins: Certain pigments can camouflage weld lines, improving the visual quality of the part.
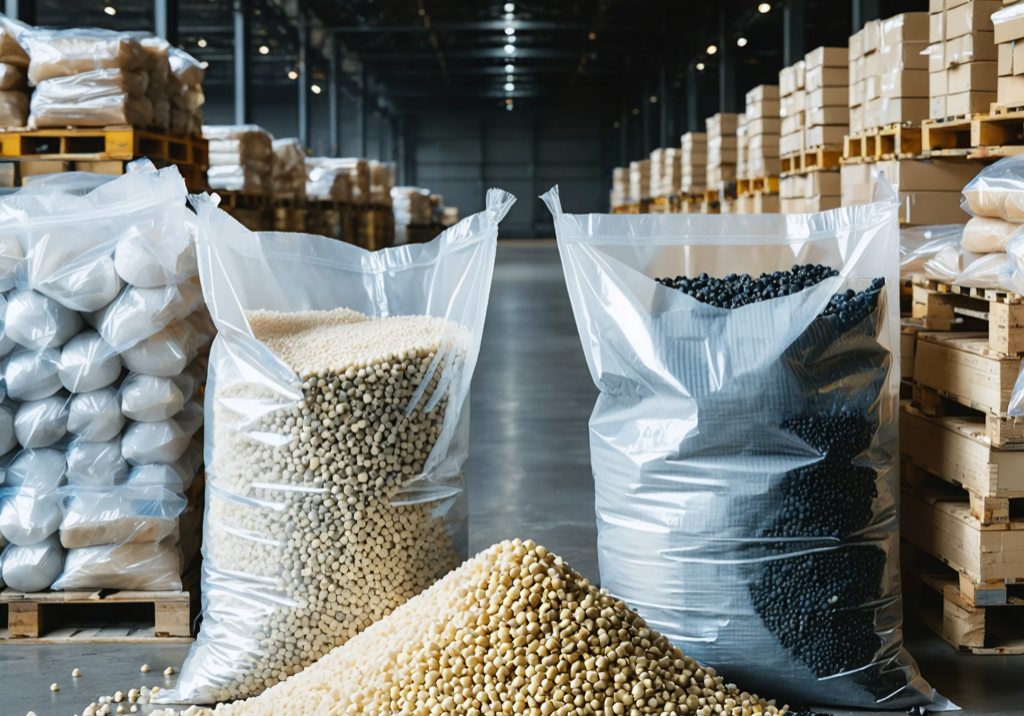
4.Control Melt Flow
Controlling melt flow ensures a smooth convergence of flow fronts.
Melt Flow Index (MFI): Select materials with the appropriate MFI for your part design.
Flow Path Length: Keep flow paths short and simple to avoid premature cooling
Balance Flow Fronts: Ensure all flow fronts travel at similar speeds to merge seamlessly.
Common Mistakes to Avoid
1. Improper Gate Location: Poorly placed gates cause uneven flow, increasing weld line formation.
2. Low Injection Speed: Slow speeds allow flow fronts to cool too quickly, preventing proper bonding.
3. Using High-Viscosity Materials: Thick materials struggle to flow smoothly, exacerbating weld lines.
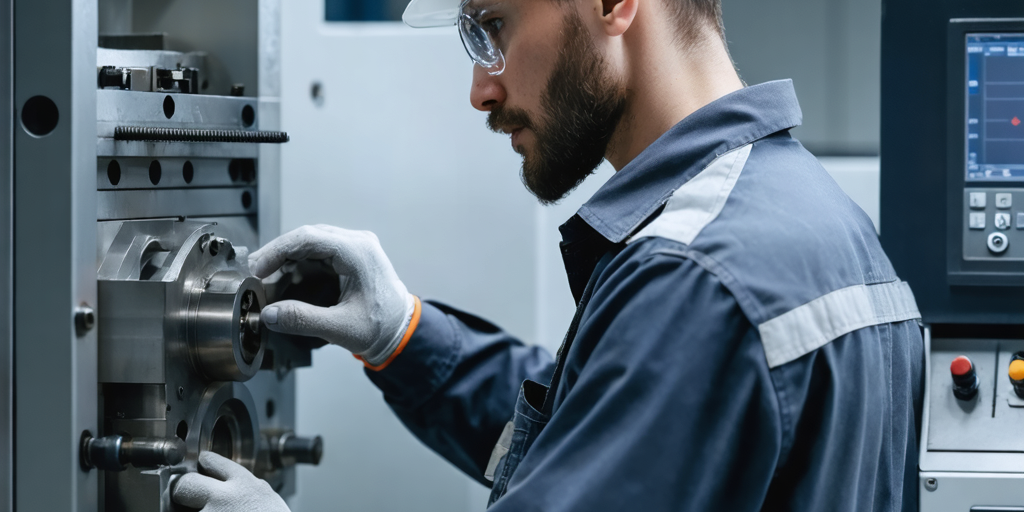
Conclusion
To avoid weld lines in injection molding, prioritize mold design optimization, adjust processing parameters, use appropriate materials, and control melt flow. Each of these strategies contributes to smoother, stronger parts free of visible weld lines.
For more expert insights on injection molding techniques, visit our resource center or contact us. Together, we can help you achieve flawless molded parts for your next project.
Post time: Dec-03-2024