Cooling polypropylene (PP) car parts evenly during injection molding can be a bit like trying to keep a cake from sinking in the middle—get it right, and you’ll have parts that are strong, warp-free, and dimensionally accurate.
To achieve even cooling for polypropylene (PP) car parts, focus on uniform mold temperature, optimized cooling channels, and balanced cycle timing.These methods help prevent warping, shrinkage, and internal stress, ensuring high-quality, durable parts.
Let’s take a closer look at each of these techniques.
Why is uniform mold temperature so crucial?
Uniform mold temperature is the backbone of consistent cooling. It’s like making sure every part of a pizza cooks evenly, so you don’t end up with burnt edges and a raw center.
Maintaining a consistent mold temperature prevents hot or cold spots, which can lead to uneven cooling and dimensional instability in PP parts. This is especially critical in automotive components, where strength and reliability are non-negotiable.
The mold temperature should ideally be set between 50°C and 80°C (122°F - 176°F) for polypropylene. This range ensures that the material flows smoothly into the mold without premature cooling, which could cause sink marks or voids. Using temperature sensors throughout the mold is a practical approach to ensure even distribution, letting you adjust as needed to avoid temperature imbalances. Temperature uniformity is especially important for car parts like bumpers, where every inch needs to cool evenly to prevent flaws.
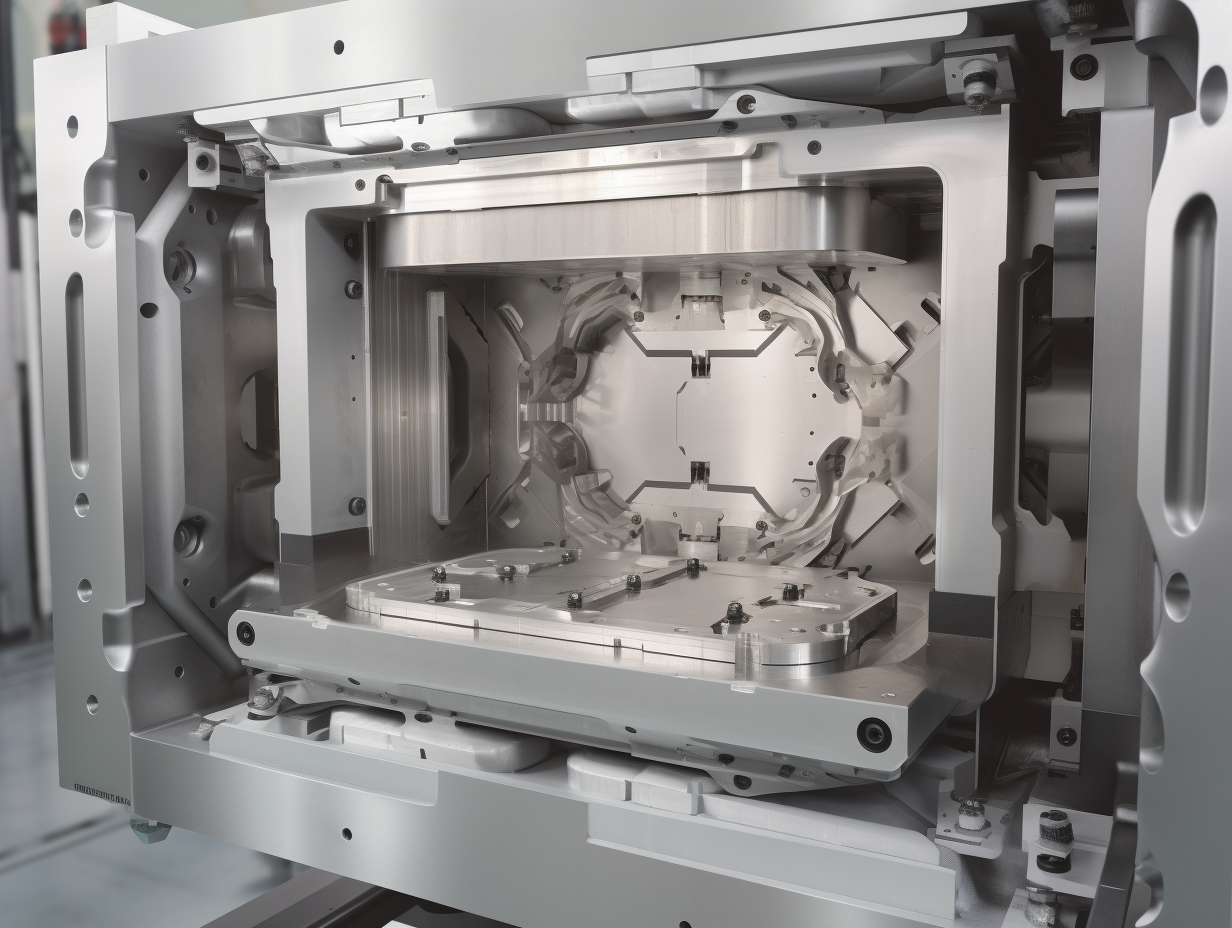
How do optimized cooling channels improve even cooling?
If you’ve ever tried to water a garden evenly with a sprinkler, you’ll understand the importance of effective cooling channels in injection molding.
Optimized cooling channels reduce cycle time by ensuring heat is evenly dissipated from the part, allowing for faster and more consistent cooling throughout the entire mold. This helps achieve smooth, uniform surfaces and minimizes shrinkage or warping.
Conventional straight-line cooling channels might not reach every nook and cranny of complex car parts, leading to uneven cooling and internal stresses. Instead, I recommend using conformal cooling channels that follow the contours of the mold. These channels allow water or coolant to flow closely around every section of the part, ensuring that even the trickiest areas receive adequate cooling. Conformal channels can also reduce cycle time, saving you production costs in the long run.
In some cases, baffles or bubblers can be added to direct coolant flow into areas that need extra attention, like thicker sections that naturally hold heat longer. It’s like giving your garden those extra few seconds of watering in the sunniest spots.
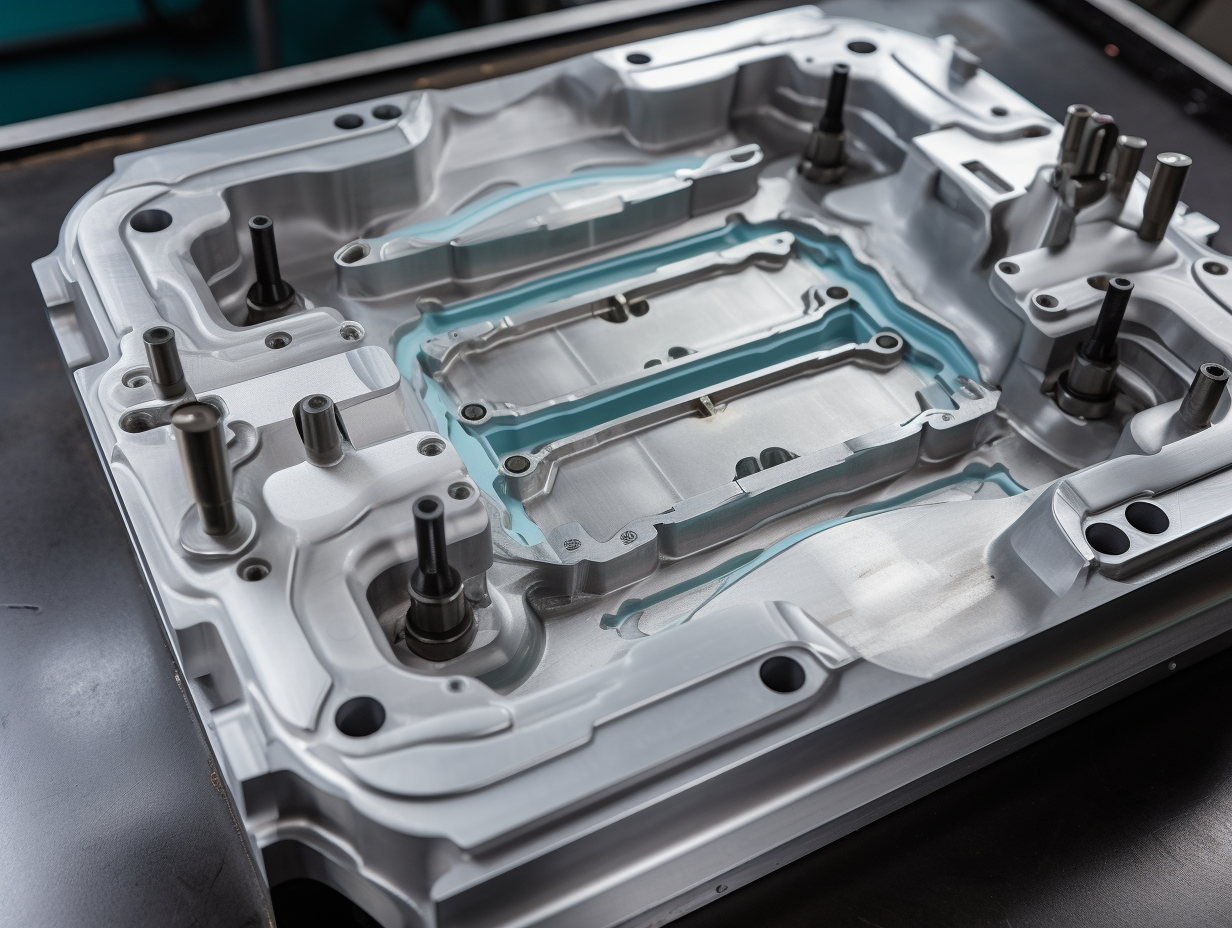
What role does cycle timing play in even cooling?
Cycle timing is all about finding that sweet spot—give the part enough time to cool, but don’t keep it in the mold longer than necessary.
Balanced cycle timing ensures polypropylene parts cool completely and evenly, reducing the risk of defects like warping, shrinkage, or stress marks. An ideal cooling time lets the part solidify while still being efficient.
To get the timing right, it’s essential to monitor the temperature as the part cools within the mold. If you eject the part too soon, it may warp as it cools outside of the mold. On the other hand, leaving it in too long wastes cycle time and can lead to higher production costs. For polypropylene, cooling times usually range from 10 to 30 seconds depending on part thickness. Precise timing is especially important in automotive applications, where precision is key to fitting and durability.
Some advanced injection molding machines offer programmable cooling cycles, allowing you to set specific times for each phase of the cooling process. This flexibility can be particularly useful when working with complex car parts with varying thicknesses, as it allows for a customized cooling profile.
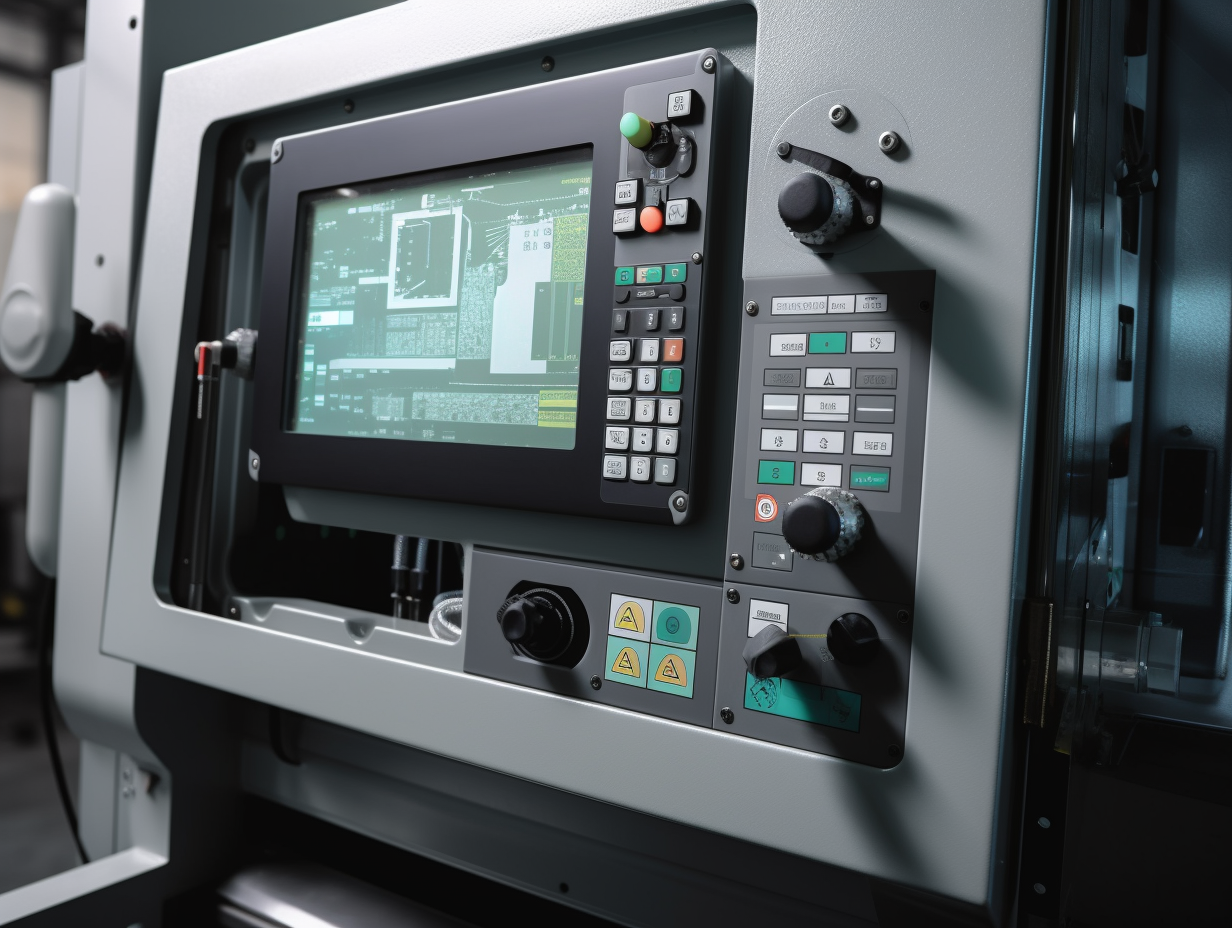
How can coolant selection affect cooling efficiency?
Coolant choice might seem minor, but it’s the unsung hero of consistent cooling.
Choosing an efficient coolant, like water or a water-glycol mix, helps achieve faster and more consistent heat transfer, making it easier to cool polypropylene parts evenly. The right coolant improves overall production speed and part quality.
While water is the most common coolant, adding glycol can lower its freezing point and improve heat transfer in high-temperature environments. Some shops even use specialized fluids for better performance, but they come at a cost. Coolant selection depends on your mold’s specific requirements, but for most PP parts, standard water-based cooling systems do an excellent job.
In particularly high-precision projects, coolant temperature can be controlled with chillers that cool the water before it enters the mold. This helps maintain the ideal temperature range, preventing fluctuations that could lead to inconsistencies in cooling and, ultimately, in the final part.
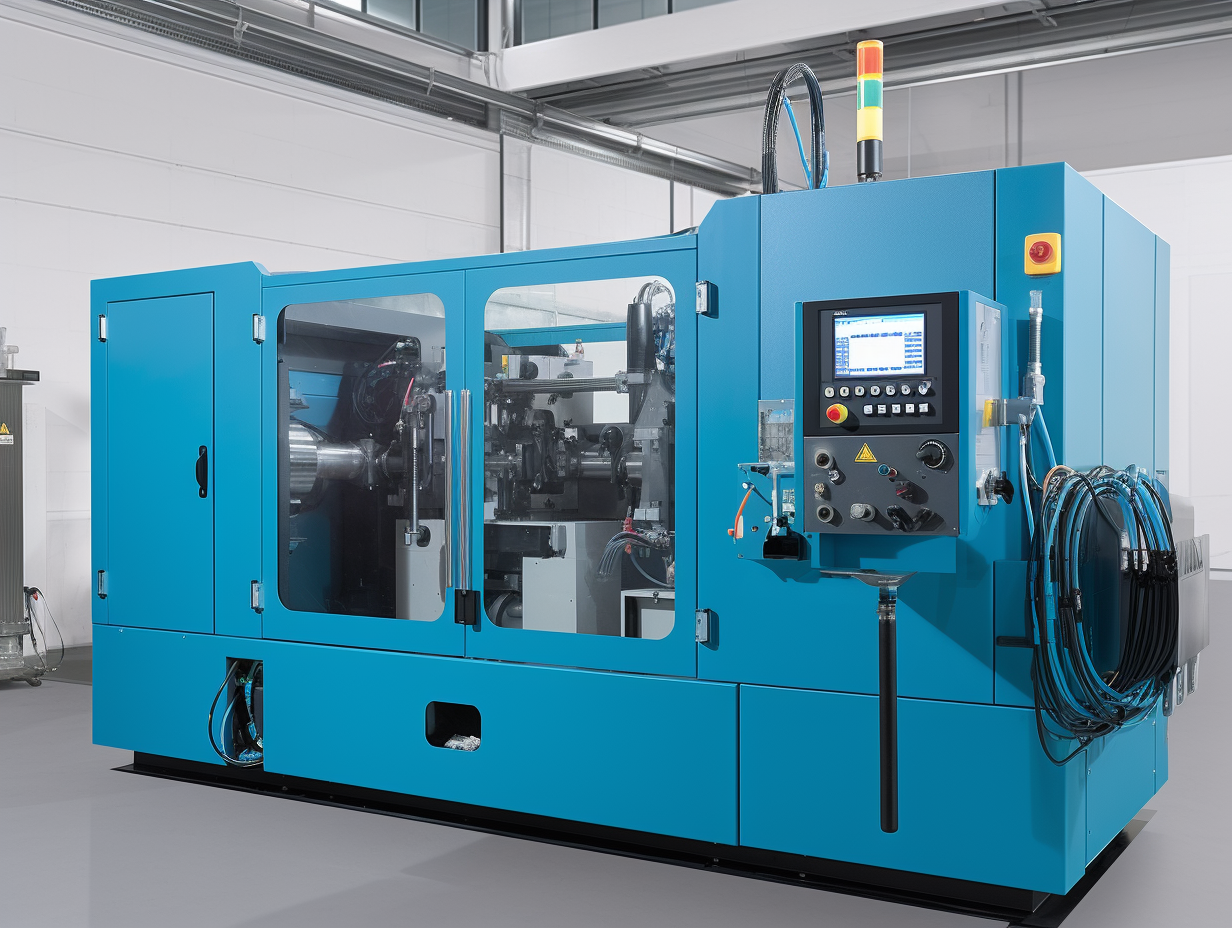
Conclusion
Achieving even cooling for polypropylene car parts comes down to controlling mold temperature, optimizing cooling channels, and balancing cycle timing. These strategies help ensure parts that meet high standards in strength and dimensional accuracy—essentials in the automotive industry.
Post time: Nov-05-2024